Last Updated: 23 October 2024
In the mining industry, the successful deployment of fatigue monitoring systems like SmartCap hinges on several factors. Workforce engagement, as part of a broader change management strategy, is essential. Other elements like clear communication, a leadership commitment to safety, and a no-discipline approach to fatigue detection are all critical components. However, our experience at Wenco International Mining Systems has shown that the single greatest determining factor in the success of these initiatives is the acceptance and engagement of supervisors.
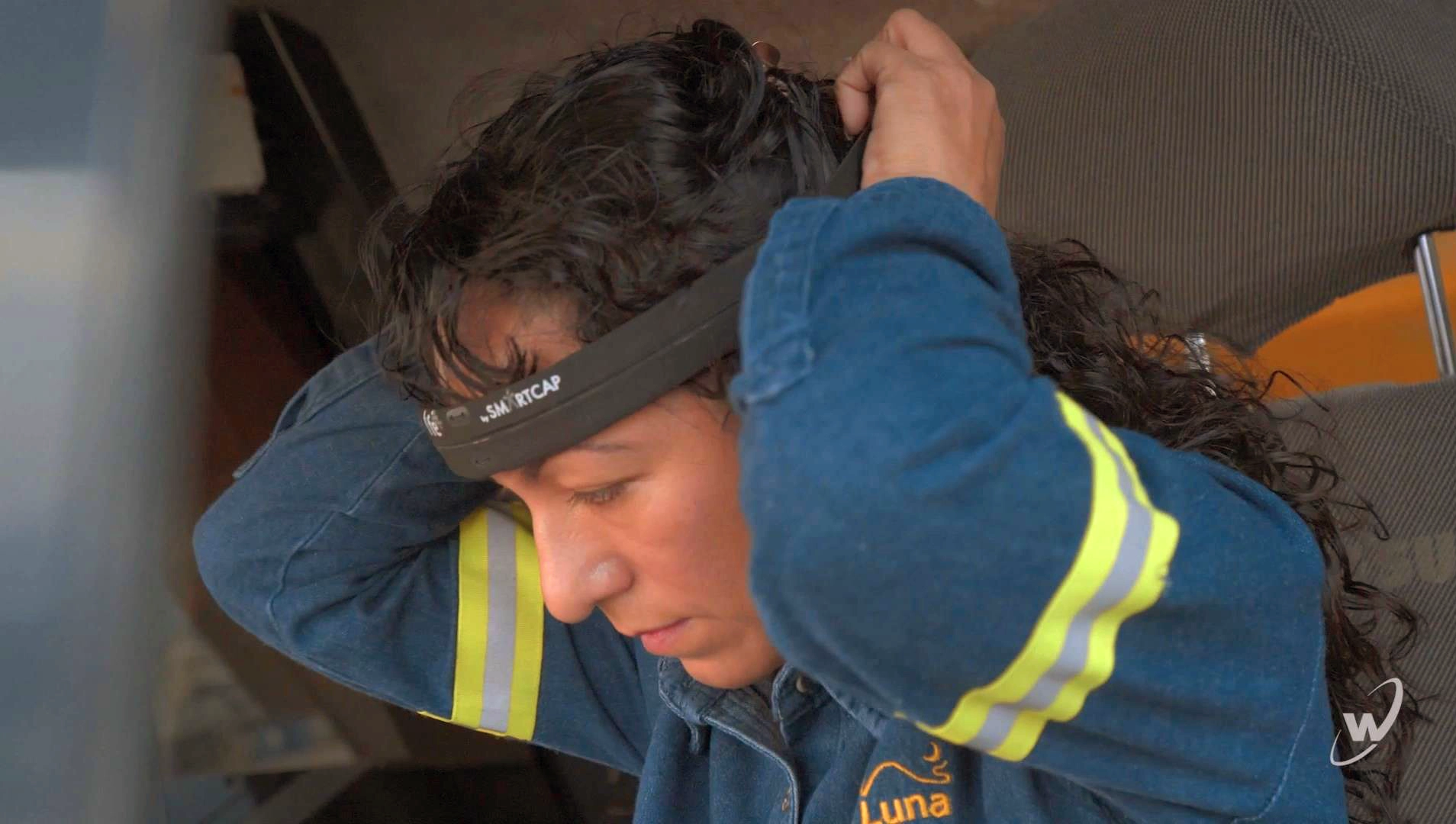
The Multifaceted Role of Supervisors
Supervisors play several critical roles in the deployment and ongoing use of fatigue monitoring systems:
- Compliance and Risk Assessment: When an “intervention alarm” is triggered, supervisors are often called on to assess the current risk and determine the operator’s fitness to return to work. This face-to-face interaction is crucial for ensuring a safe working environment for the entire workforce.
- Influencing Operator Acceptance: Beyond compliance, supervisors are instrumental in addressing operators’ concerns about being monitored. They help mitigate the “big brother” fears by reinforcing the safety culture and demonstrating that the technology is not for disciplinary purposes but for the well-being of the operators.
- Encouraging Self-Management: Supervisors encourage operators to manage their fatigue proactively. By responding to early warnings from SmartCap, they can prevent the progression to fatigue risk alarms.
- Reinforcing Training and Guidance: Supervisors also play a key role in reinforcing training and providing ongoing guidance to operators, ensuring that they understand expectations for the use of the fatigue monitoring tool and address any issues the operators might be facing.
Challenges in Securing Supervisor Buy-In
Despite their critical role, securing supervisor buy-in can be challenging. Supervisors are already burdened with numerous responsibilities, including meeting production targets and ensuring safety. They are often the first to arrive for their shift and the last to leave, making the addition of an ongoing fatigue monitoring initiative seem like just another task to juggle.
Supervisors may also feel out of the loop if they were not involved in the decision to implement the particular fatigue monitoring system. They might also feel unprepared to conduct face-to-face assessments, fearing increased liability and exposure. Additionally, the perception that pulling trucks over for fatigue checks could hinder production targets might add to their reluctance.
Best Practice for Securing Supervisor Buy-In
To overcome these challenges, we’ve observed that clients that include each of the below steps enjoy the greatest engagement from the team of supervisors:
- Engage Supervisors Early: Involve supervisors from the outset of the initiative to ensure they understand its importance and their role in its success.
- Provide a Comprehensive Overview: Offer a clear overview of the entire initiative, including points of escalation, to ensure supervisors are well-informed.
- Collaborate on an Intervention Script: Work with supervisors to develop a script for intervention alarms, making the process straightforward and less intimidating.
- Simplify the TARP: Simplify the Trigger Action Response Plan (TARP) wherever possible to make it clear and easy to follow.
- Role Play and Feedback: Conduct role-playing sessions and encourage feedback to help supervisors feel more comfortable with their responsibilities.
- Refresher Coaching: Provide routine refresher coaching to keep supervisors up-to-date and confident in their roles.
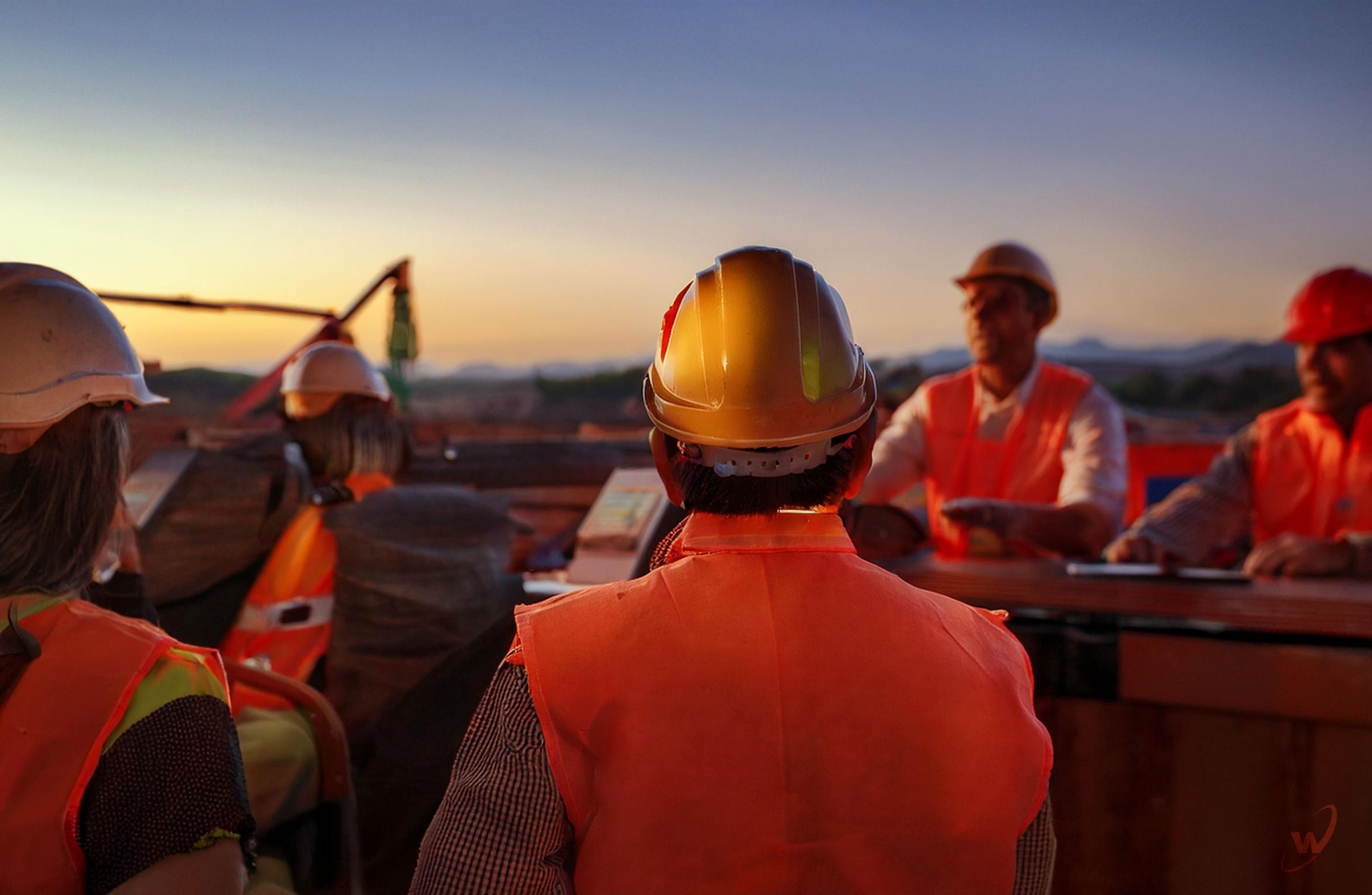
The Impact of Supervisor Engagement
When supervisors are engaged, the outcomes of fatigue monitoring initiatives improve significantly. For example, with strong supervisor engagement, operators are more likely to respect early warning alerts and take self-management actions, addressing potential fatigue issues before they escalate. This proactive approach leads to a noticeable reduction in fatigue alarm events over time.
We also see significant reductions in distraction-related incidents. This is in-part a consequence of having a more alert workforce, given the link between fatigue and distractibility, though is also due to a more engaged and attentive workforce. This shift in mindset facilitated by supervisors also contributes to a decrease in human-error incidents - the catch-all incident category where specific cause is unknown.
In essence, the presence of engaged supervisors transforms the fatigue monitoring initiative from a mere compliance exercise into a comprehensive safety enhancement program, leading to a more engaged, more alert and safer workforce, and to more efficient operations.
Published: 23 October 2024
Last Updated: 23 October 2024