There's no surprise in calling rework a drain on the mining industry. It’s a drain by definition. Every time operators need to do the same job again (and again and again), every mine KPI suffers — productivity, efficiency, and even safety.
Yet, rework is treated as a normal cost of business that mines have to live with every day. The construction industry averages 7.1% of its work hours and $178 billion on rework each year. That’s almost one hour in each 12-hour shift dedicated to fixing mistakes that should have been done right the first time. "I worked for one mining company who named a 1,200-yard-longramp the ‘million dollar ramp’ because it took three times for the dozer operators and surveyors to get it correct,” says Hal Galbraith, manager of the Wenco Centre of Excellence. With Machine Guidance, areas if weakness that might otherwise contribute to billions in rework each year are addressed to make it an anomaly.
It’s not just the wasted time and effort, either. Rework comes with a long line of secondary costs as well. If a dozer has to redo the surface of a haul road, the mine has to consider the operator’s time, the time it takes to close the road and set up a detour, the additional fuel needed to get the job done, the additional wear-and-tear on the dozer, and more.
There’s a safety cost to rework as well. All heavy industry comes with the risk of injury, and doubly so if operators have to repeat their work just to get the job done. Earthmoving requires surveyors to assess elevation and confirm compliance to design as well, adding another layer of risk every time they need to step on the bench and take another round of measurements.
While the burden of rework is notable for large and small operations alike, it is often more severe for contractors. Without the ability to eat the inefficiency or earn back the costs with a highly productive shift, contractors are typically hired to do a fixed job for a fixed fee. Any unnecessary work cuts into their profit margins, making rework an even more insidious problem.
Obviously, no one wants to do the same thing over and over to get the same result. (By some measures, it’s a definition of insanity.) But, what can mining operations and contractors do about it? In most situations, three key factors are fundamental to making rework an anomaly instead of business as usual.
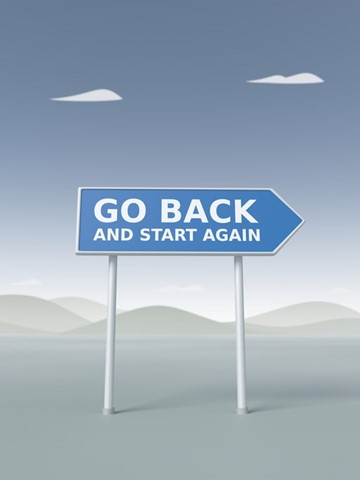
Plan to Work, Then Work to Plan
First and foremost, effective planning can transform the amount of rework needed for any mine activity. Mines that take the time to record accurate elevation and other topography measurements, develop clear designs for work to be done, and create a clear strategy for the job tend to fare better than sites trying to cut and fill on the fly.
“It all starts with a good plan,” says Galbraith. “It wasn’t always this way, but most mines by now have gotten the message. Even with a simple project, it's poor practice to dive in and go. The extra time to develop accurate designs and accurate plans can save hours — and tens of thousands of dollars —down the road.”
Communicate, communicate, communicate
Second only to planning, communication can make or break the efficiency of an earthmoving project. Even the best plan is useless if no one knows about it. “Establishing clear and simple communication processes is a zero-cost way to improve safety and reduce rework,” says Galbraith.
With the ability to share plans instantly between the office and operators, machine guidance benefits are realized in safety through communication of hazard alerts in conjunction with plan details, and efficiency through feeding as-built data back to the office in real-time. A heightened capacity to communicate critical information regarding hazards, as built-data and plan compliance, enables operations to dramatically lower the volume and impact of rework.
Use the best tools at your disposal
Industrial equipment is fundamental to modern mine construction, but it still has major issues with accuracy and data collection — issues that lead to major rework. Fortunately, data technologies like machine guidance have filled those gaps in recent years, removing the need for operators to cut and fill the same area again and again.
“Computer-based designs make a huge difference,” says Galbraith. “By loading a .DXF file into a machine guidance system and following the onscreen guidelines, dozer operators don’t have to stress about doing their job right. The computer gives them real-time feedback, so they know every pass is in compliance with the design— the first time.” Also noted by Galbraith were the safety advantages that emerge when computer based designs account for hazards. With machine guidance, operators can do their job both more accurately and more safely with plan specific alerts.
The real costs of rework
Rework is a major inefficiency and — when you consider the added fuel, wear-and-tear, safety, and missed opportunities — its real costs make it a real problem for mines and mine contractors. Yet, proper planning, communication, and technology can make its impact little more than a rounding error for most operations.
So, at mines and contractor-run operations where rework remains a problem, there’s an obvious question: How long can you keep doing the same thing over and over again — and expect a different result?
Want to know more about high-precision machine guidance technology? Download The Wenco Guide to Machine Guidance for Mine Contractors.
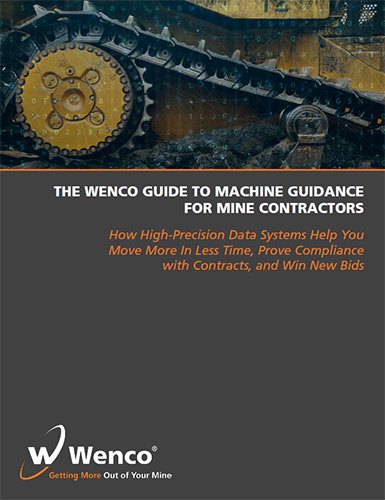
Inside, you'll learn about...
- How machine guidance works
- The top 3 ways contractors use machine guidance to raise their profitability
- The most common questions users have about machine guidance
- How this simple technology lowers wait times, automates data collection, and helps you land more contracts than ever before
Get The Wenco Guide to Machine Guidance for Mine Contractors now to learn how to improve your profitability today.