By the 1970s, large drilling machines had become widely used in the mining and quarry industries. These drills would move from one hole location to another by one of two means: either surveyors would mark each hole location for the entire pattern or drill operators would manually measure the distance between each hole location. (This latter way gave far less accurate hole spacing.) Since then, with the use of global navigation satellite system (GNSS), the mining industry has had the ability to navigate machines to drill holes with high precision, without needing surveyors to mark hole patterns out in the field. All pattern designs can now be done within the office and sent to the drill electronically, allowing a seamless operation between the engineering design and the actual drilling of holes. The Wenco Drill Navigation system fulfills this basic requirement by helping the machine operator be able to quickly and precisely move the drill to each hole location in the pattern. In doing so, the system eliminates the need for tedious field survey work and delays in laying out planned drill patterns. Setup of the drill is also faster, as the system provides real-time feedback about actual mast position and bearing during operation. The Wenco Drill Navigation system also automatically gathers as-drilled information and other operational information, which are extremely valuable for blasting personnel. Inside the cab of the drill, the operator sees two main views on the Wenco Drill Navigation screen. The first view is the main navigation screen, as seen in this screenshot.
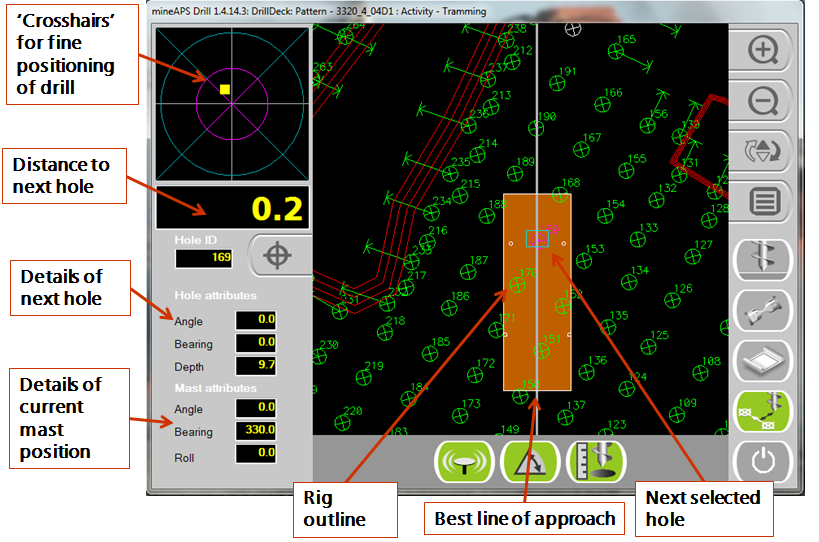
This view gives the operator distance to the selected hole location, best line of approach, target depth, and any angle hole information. It also allows the operator to accurately place the bit of the drill on the designed hole location. As the drill approaches the hole, the crosshairs zoom in on the hole location, giving the operator the ability to exactly place the drill bit at the designed location. Once the drill operator is ready to start drilling, the second view is activated, as seen in this image.
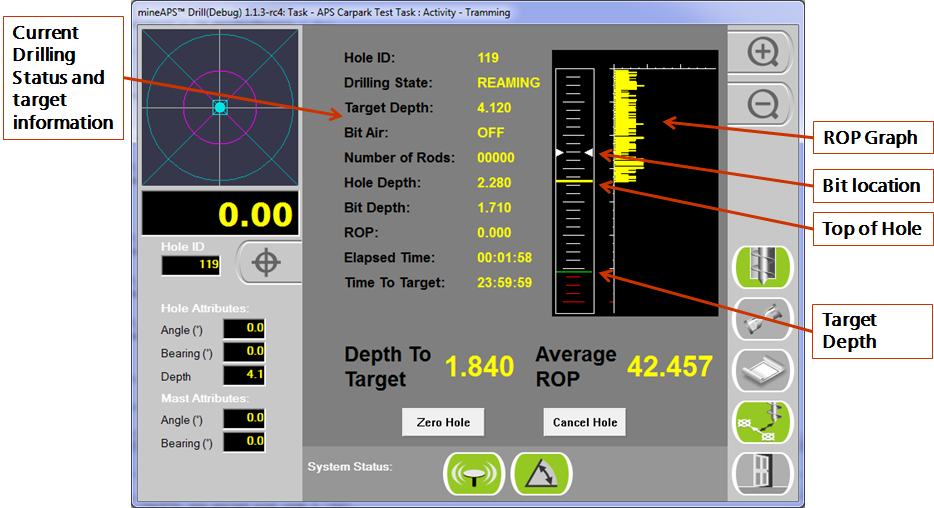
This screen gives the operator important as-drilling attributes, such as target depth, rate of penetration (ROP), and number of rods being used. In addition, the operator is able to graphically see the depths of the bit and the top of the hole in relation to the target depth. Within Wenco's office software suite, the mine's engineers are able to see a visualization of the as-drilled hole pattern, as seen below.
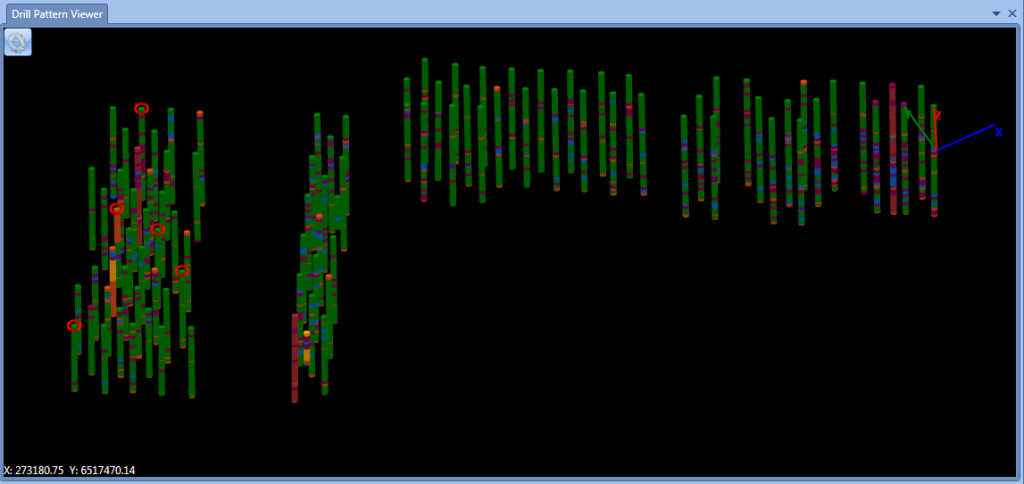
Each hole can be selected to see detailed information within a particular segment of the hole, as seen here.
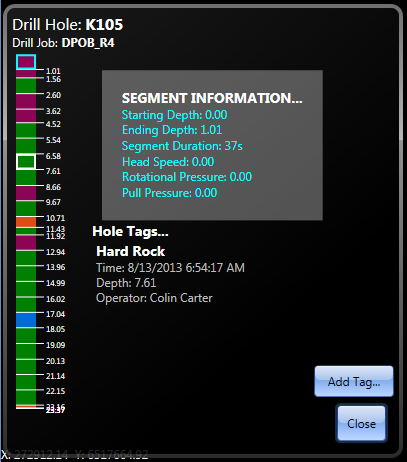
With even just these features described, mines can realize several key benefits. First, there's no longer a need to have surveyors marking holes for a drill pattern. Second, actual as-drilled hole information can be seen by blasting personnel, allowing them to load holes accordingly with explosives. Knowing the actual hole spacing and ROP information, fragmentation can be improved and become more consistent. And third, with the operator being able to drill each hole to a targeted elevation, the benches of the mine become more consistent. All of these can give a mine a quick return on investment and easily justify purchasing the Wenco Drill Navigation system.These features form the basis of the Wenco Drill Navigation system, but there are more advanced features that can give mines even more value — things like integration of safety aspects of machine proximity and fixed hazard warnings. Also, there's the ability for the operator to create notes, or hole tags, allowing later analysis of things like voids discovered or coal seam locations. A full reporting suite is available to monitor all aspects of the drilling operation. Wenco's development teams are currently focused on adding consumable tracking and strata recognition. All these features add even more capabilities to the already powerful Wenco Drill Navigation system.