Mines know the benefits of standalone machine guidance. Cost. Flexibility. Sites can drop a system on a contractor machine and set it to work — no muss, no fuss. Some mines wonder why they'd ever need to integrate their fleet management and machine guidance systems at all.
It's true, standalone systems work great (even Wenco has a standalone option). Any high-precision system that helps you locate accurate material types and minimize rework is a smart choice.
But, don't underestimate the benefits that come with integration.
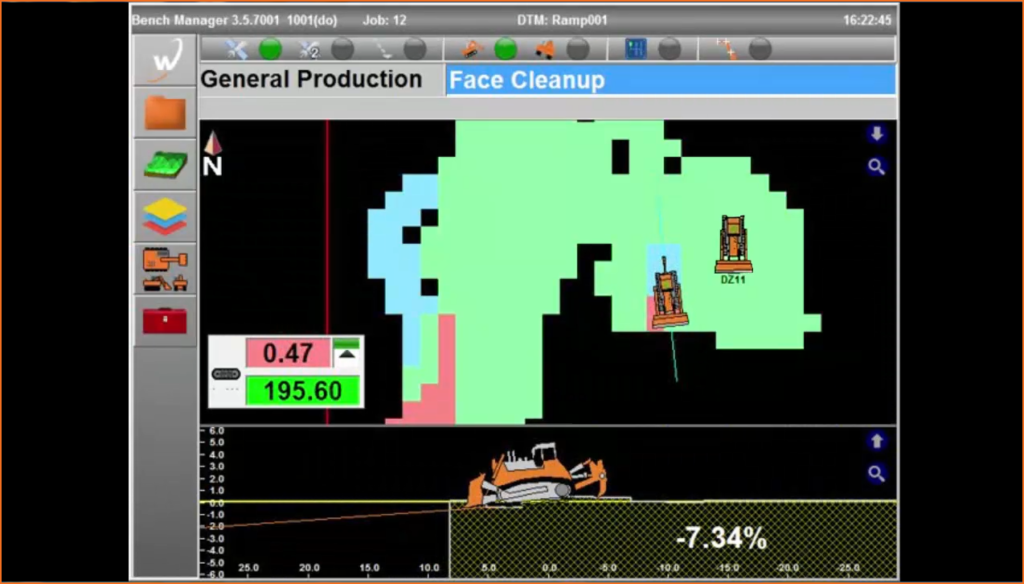
With an integrated system, all your equipment stays in sync. Each unit works from the same database so they share information easily, whether they're shovels or dozers, loaders or light vehicles. There's no need to export data, convert it to another format, then upload it into another system. With a tool like Wenco's BenchManager, it all happens automatically in real time.
This kind of setup has serious advantages. Most importantly, it improves safety. Any unit running Wenco's integrated BenchManager system sees every other unit connected to the fleet management system. The onboard screen shows their position, elevation, and current activity in real time. With that knowledge, dozers can easily maneuver around hazards and other equipment, even in foggy or dusty conditions. With a standalone system, equipment is confined to viewing only units on the same network. Any vehicles outside it need another way to stay safe on site.
Integration also lets units auto-sync their data so they always work from current, accurate surfaces. This function helps your machines work together. If both a shovel and a dozer run BenchManager, each unit updates the other as they reshape the site. If a shovel cuts too deep, the dozer can see it and fill it to the proper target. If needed, all high-precision units can even see the makeup of dig blocks. If this equipment used two different databases, a dispatcher would need to transfer and convert surface coordinates manually, wasting valuable production time.
The biggest advantage of integrated machine guidance, though? The future. Wenco and Hitachi are constantly working on new technologies to make mines smarter. Upgraded machine health tracking. Business intelligence tools. Peer-to-peer predictive equipment interaction. When each new product launches, any mine using the Wencomine system can access these tools immediately. There's no waiting for further development to make machine guidance work and there's no concern about reduced functionality.
Every modern mine has a wide range of equipment. Shovels and dozers, graders and draglines — they all need to work together to keep the haul cycle turning. Integrated machine guidance keeps them connected in real time. And, it lets your mine take full advantage of its fleet management features — the ones currently available and the ones still to come.