Lately, every mining executive we connect with focuses on leveraging data and interoperability to drive productivity and profitability within their operations. They see how the industry is changing from an "ore-push" to a "customer order-pull" model in which market demands influence production. This change is behind the drive to connect together the systems used throughout entire operations — end to end — to better plan and execute the delivery of product.The big issue with this approach is that a lot of mines operate in silos, putting together data in spreadsheets. To change to a demand-driven, customer-centric model, mines need to integrate their operations and their systems — from planning to pit to plant to port (or "pit to port", for short).With the advent of automated systems across the pit-to-port spectrum, mining companies are even more motivated to get the data and systems interoperability model correct. Once they do, they can take advantage of that integration when autonomous systems come online.
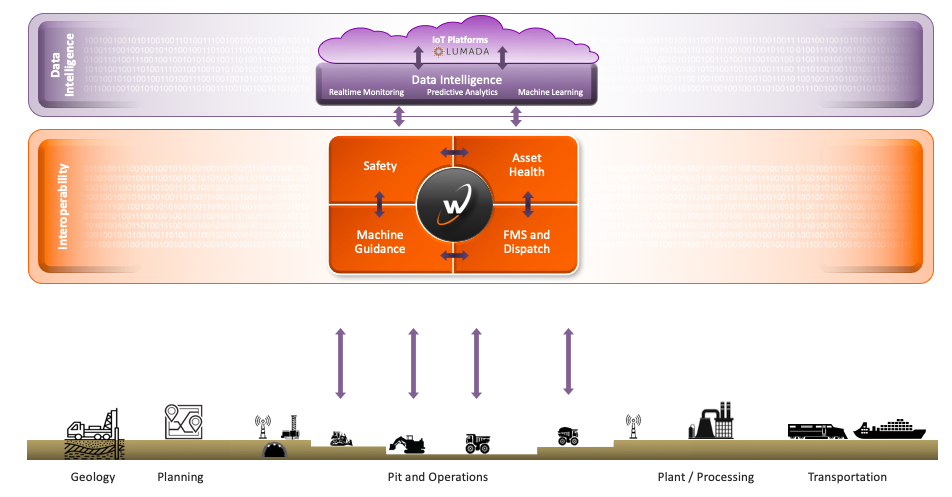
Interoperability Requires Open Standards
With the future of interoperability for data and automated systems in mind, our Executive Vice-President, Corporate Strategy Eric Winsborrow recently spoke at the Hitachi Social Innovation Forum (HSIF) in Sydney. His presentation, How Australia Will Lead the Future of Mining: Interoperability, Autonomy and the Connected Mine, paints a rich future coming from these disruptive technologies. But, it also highlights a major issue with current systems: Changing to a customer-centric model requires different technologies from different vendors to work interoperably in different situations. As it stands, most systems struggle to share their data at all. There are no open standards in place that let them do it.Most sites already have significant investments in systems and equipment throughout their pit-to-port operations, typically from a variety of vendors. The operations department alone may use one company's system for fleet management, another for machine guidance, and equipment from three or four different manufacturers.As long as mines operate in silos, the different standards and protocols used by each of these systems don't matter. But, with such a big push toward interoperability as a precursor to autonomy, mines are beginning to understand the need for an international standard that enables their systems to work with one another.The Problem With Proprietary Systems
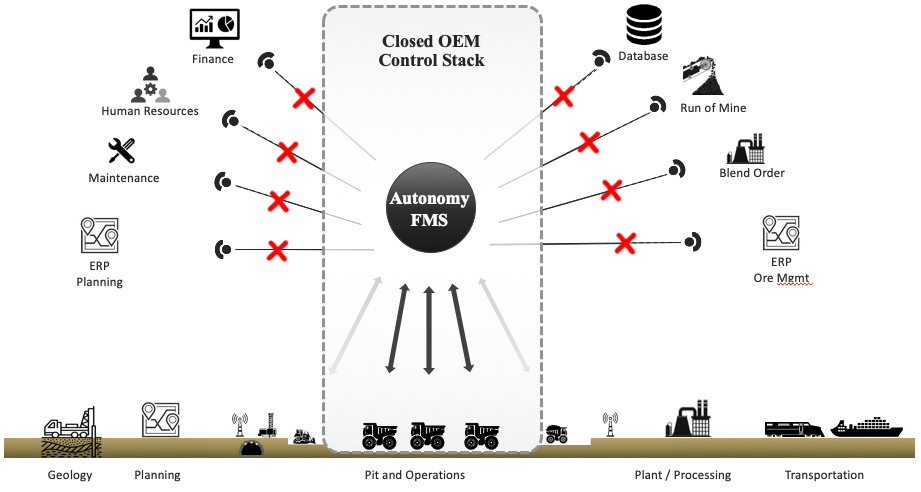
Before mining systems can work autonomously, they need to freely communicate, share data, and let that data affect each other. To do so, they require a common interface and protocol — they need to speak the same language.In theory, a site that only uses systems and equipment from one vendor could link them all together and call their mine interoperable. But, no site in the real world has systems and equipment from only one vendor. They all use an assortment of trucks and shovels, machine control systems, communications protocols, and other solutions from many different providers. No one vendor offers a complete pit-to-port suite of solutions for mining, let alone the best-of-breed in each area.Without a common standard and interface that enables these different systems to communicate, every time a mine wants to make two of these systems work interoperably they need to create an entirely new interface. New interfaces mean high costs for development, implementation, training, change management, and troubleshooting. If that mine wants to use a system from yet another vendor, the issue doubles.Of course, technology vendors understand the benefit of enforcing their own proprietary standards. They think they can shore up loyalty among their installed base and control an even larger share of the available market. But, they miss the entire point of pit-to-port interoperability and autonomy in the first place — to save their customers money.How many millions are required in interface development and support before mines actually start saving? How much will it cost to use existing systems and infrastructure alongside new autonomous technology?
An Open Approach to Interoperability
Closed systems aren't necessary, though. System developers can follow open standards instead. Using an open standard interface, mines can maintain their investment in the technology and infrastructure they've built up over decades and, simply, insert an autonomous system alongside it when the time comes. A fleet management system already installed to command and control a mine's crewed fleet could share data across an ISO-standard interface to do the same for autonomous vehicles.Regardless of the OEM vendor, any site could freely connect its system to equipment through this standard interface.
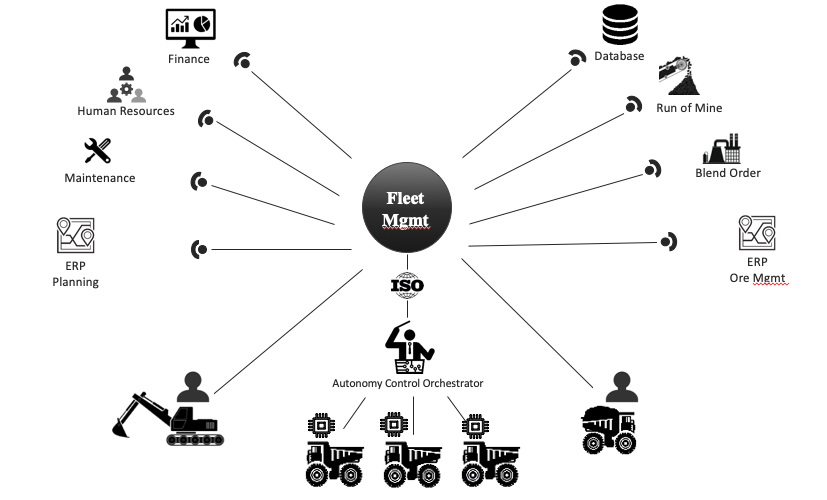
This scenario gives customers a lot of advantages. Obviously, it's easier to manage a common interface than multiple proprietary ones. It also allows a suite of mining systems — fleet management, machine guidance, asset health, collision awareness, and more — to access contextual information alongside operational data, which helps with planning and decision-making.Open standards also provide an opportunity for new companies to enter the market who may not have the same clout as one of the Big Three OEMs. With an open standard, these upstart companies can participate without getting locked out of workflows to the benefit of OEMs more than their customers. Sure, new entrants always pose competition to industry incumbents, but innovations like autonomous mining always come with risks to the old guard. Besides, the alternative is much worse. Existing vendors who resist open standards and, instead, try to fight them tend to get forgotten as a disruptive technology transforms the industry from the ground up.
The Path to Mining 4.0
At HSIF, a lot of mining industry leaders openly echoed the call for progress toward autonomous solutions. But, a completely autonomous solution doesn't happen all that once — it happens in phases. Before autonomy can take hold, mining needs its existing solutions to work together in the first place. To create this kind of open interoperability, mining needs an open standard that supports the flow of data back and forth throughout all its systems. Only then can the industry make real headway toward an ultimate vision like Mining 4.0.
Interested in learning more about the path to digital mining and Mining 4.0? Please contact us at info@wencomine.com or 604-270-8277.